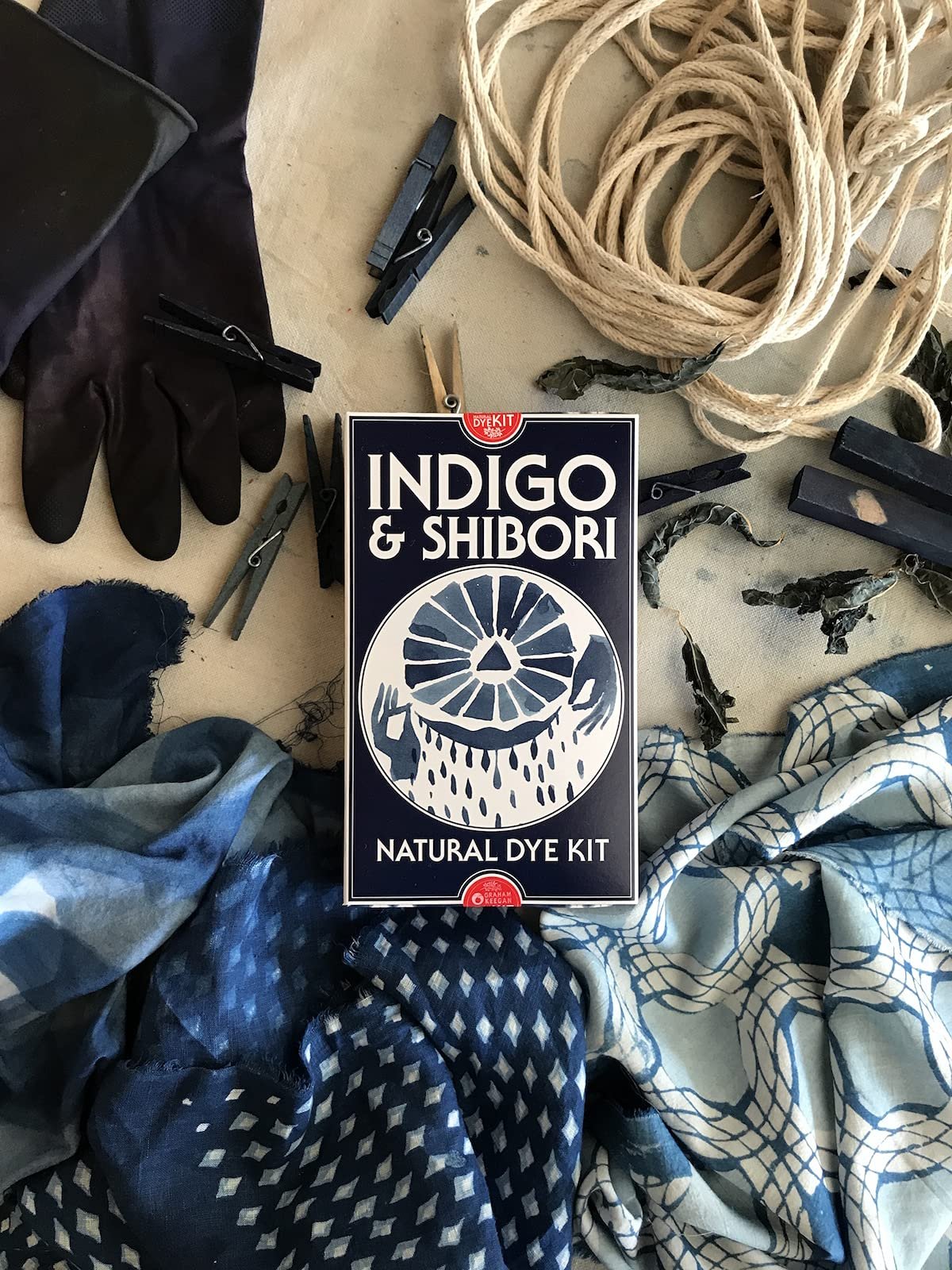
INDIGO DYEING : Questions & Answers
Some of the questions on this page are specific to indigo dyeing using our Indigo & Shibori Natural Dye Kit, but many are applicable to indigo dyeing more broadly!
Your dye kit comes complete with a load of supplies and materials that you can use to make designs on fabrics. Some parts of the process are complex and we may not have had room in the printed instructions included to go in depth.
If you have a question that has not yet been answered to your satisfaction, ask away!
USE KEYWORDS TO SEARCH FOR ANSWERS TO YOUR QUESTIONS
The following is an index list of each Question and Answer title, click on the title to read the corresponding Q&A, or simply use search terms in the search box above to see if your question has been answered!
-
DIP TECHNIQUE
- Jul 26, 2023 Avoiding Fading
- Jul 26, 2023 Dipping Resist Pieces
- Jul 26, 2023 Maintaining Your Whites While Rinsing
- Jul 25, 2023 Dyeing Over Multiple Days
- Jul 25, 2023 Avoiding Sediment
- Jul 25, 2023 How Sediment Affects Your Dyeing and the Importance of Proper Rinsing
- Jul 25, 2023 Tips for Using Rice Paste in a Ferrous Vat
- Jul 25, 2023 Tips for Getting the Darkest Blues
- Jul 25, 2023 Suggestions for Uneven Coloration
- Jul 25, 2023 Rinsing Stencil Print Between Dips
- Jul 25, 2023 Number of Dips for Different Shades of Indigo
- Jul 20, 2023 Avoiding Sediment in the Ferrous Indigo Vat
-
DYE GARDEN QUESTIONS
- Jul 26, 2023 Starting Indigo Seeds Indoors Versus Outdoors
- Jul 25, 2023 When to Plant Indigo Seeds
- Jul 25, 2023 Indigo Seed Propagation
-
GENERAL INDIGO DYEING QUESTIONS
- Jul 26, 2023 Calculating Amount of Indigo Needed
- Jul 25, 2023 Dyeing Protein Fibers in a Natural Indigo Vat
- Jul 25, 2023 Dyeing Stretch Fabric with Natural Indigo
- Jul 25, 2023 Ferrous Vat Longevity
- Jul 25, 2023 Shelf Life of Natural Indigo and “Pasting-Up” Your Powder
- Jul 25, 2023 Toxicity of Indigo and Indigo Dyeing
- Jul 25, 2023 Indigo and Splatter Dyeing
- Jul 25, 2023 Indigo and Cotton Velveteen
- Jul 25, 2023 Indigo and Polyester
- Jul 25, 2023 Over-dyeing with Indigo
- Jul 25, 2023 Is Indigo Dye Okay for Sensitive Skin, Is it Safe Enough to use on Baby Clothes?
- Jul 25, 2023 Light and Pale Shades of Indigo
- Jul 25, 2023 Fixing Indigo Onto Fabric
- Jul 25, 2023 Materials and Fabrics Suitable for Indigo Dyeing
- Jul 25, 2023 Disposing of a Ferrous Indigo Vat
- Jul 25, 2023 Large Container e.g. Trash Can Vat
- Jul 20, 2023 Dye Vat Capacity
-
INDIGO LEAF EXTRACTION
- Jul 25, 2023 Making a Ferrous Vat with Fresh Indigo Leaves
- Jul 25, 2023 Clarification on Indigo Extraction
-
INDIGO VAT TIPS & TROUBLESHOOTING
- Jul 26, 2023 Is the Fermentation Vat the Best Vat?
- Jul 26, 2023 Indigo Vat Troubleshooting: No Longer an Odor
- Jul 26, 2023 Indigo Vat Troubleshooting: Dark Blue Vat
- Jul 26, 2023 Indigo Vat Troubleshooting: Greenish Tint
- Jul 26, 2023 Avoiding Fading
- Jul 26, 2023 Waiting 24 Hours Between Mixing and Using Your Indigo Vat
- Jul 26, 2023 Quantity of Indigo Paste in a Vat
- Jul 26, 2023 Making a Long Term Vat
- Jul 25, 2023 Indigo Flower Comes and Goes
- Jul 25, 2023 Using Pencil to Make Marks on Fabric - Does Graphite Affect the Vat?
- Jul 25, 2023 Under-Reduced Fructose Vat
- Jul 25, 2023 Troubleshooting a Different Vat Recipe
- Jul 25, 2023 Avoiding Sediment
- Jul 25, 2023 Indigo Vat Troubleshooting: Recipe Quantities for a Large Vat
- Jul 25, 2023 Sharpening Your Vat
- Jul 25, 2023 Stirring Your Vat
- Jul 25, 2023 Adding More Pigment to a Fresh Leaf Extraction Vat
- Jul 25, 2023 Making a Vat for Pale Dyeing
- Jul 25, 2023 Sizing Up Your Vat
- Jul 25, 2023 Indigo Vat Troubleshooting: Lye and Hydrosulfite
- Jul 25, 2023 Recipe for Pickling Lime and Fructose Vat
- Jul 25, 2023 Thoughts on Using Soda Ash and Spectralite Instead of Iron and Lime in Making a Dye Vat
- Jul 25, 2023 Giving Your Vat Enough Time to Set Up
- Jul 25, 2023 Switching Reducing Agent and pH Combo When Sharpening Your Vat
- Jul 25, 2023 Vat Temperature
- Jul 25, 2023 Precision of pH for Ferrous and Fructose Vats and Indicators of Under or Over Reduction
- Jul 25, 2023 Forms of Indigo that Work in a Ferrous Vat Recipe
- Jul 25, 2023 Indigo Vat Troubleshooting: Sludge and Sediment
- Jul 25, 2023 Indigo Vat Diagnosis: Vat Color, Flower, and pH
- Jul 25, 2023 Iron Vat Temperature
- Jul 25, 2023 Dissolving Lime in an Indigo Vat
- Jul 25, 2023 Reviving a spoiled or 'oxidized' indigo dye vat
- Jul 25, 2023 Mixing and Combining New Vat Ingredients with Old or Spent Vats
- Jul 25, 2023 Indigo Vat Mixing Temperature
- Jul 25, 2023 Weak Vat, Old Vat and Vat Health Restoration
-
PRE AND POST-DYE TREATMENTS & TIPS
- Jul 26, 2023 Preventing Crocking and Dyeing Large Fabrics Like Bedding
- Jul 26, 2023 Avoiding Fading
- Jul 26, 2023 Rinsing in Still Versus Running Water
- Jul 25, 2023 How Sediment Affects Your Dyeing and the Importance of Proper Rinsing
- Jul 25, 2023 Troubleshooting Strange Fading Patterns and Discoloration
- Jul 25, 2023 Suggestions for Uneven Coloration
- Jul 25, 2023 Fabric Drying Stiff and Crispy Post-Dyeing
- Jul 25, 2023 Indigo Post-Dye Rinse: Purposes and Options
- Jul 25, 2023 Protecting Your Indigo-Dyed Pieces From Fading: Proper Scouring and Soy Milk Treatment
- Jul 25, 2023 Sun Fading of Indigo
- Jul 20, 2023 Best Way to Dry Indigo Dye
-
QUESTIONS ABOUT OUR INDIGO & SHIBORI DYE KIT
- Jul 26, 2023 Waiting 24 Hours Between Mixing and Using Your Indigo Vat
- Jul 25, 2023 Scaling Down Vat Size
- Jul 25, 2023 How Much Fabric Will the Natural Indigo & Shibori Dye Kit Dye?
- Jul 25, 2023 Ferrous Vat Longevity
- Jul 25, 2023 Components in the Natural Indigo & Shibori Dye Kit
- Jul 25, 2023 Indigo Form in the Natural Dye Kit
- Jul 25, 2023 Indigo Kit and Dyeing Large Items
- Jul 25, 2023 Light and Pale Shades of Indigo
- Jul 25, 2023 Scent of Natural Indigo
- Jul 20, 2023 Dye Vat Capacity
-
RICE PASTE
- Jul 26, 2023 Dipping Resist Pieces
- Jul 26, 2023 Pastry Cones for Applying Rice Paste Resist
- Jul 26, 2023 Indigo Resist Screen Printing
- Jul 26, 2023 Rice Paste Resist Longevity
- Jul 26, 2023 Destabilized AKA De-Fatted Bran in Rice Paste Resist
- Jul 25, 2023 Tips for Using Rice Paste in a Ferrous Vat
- Jul 25, 2023 Rinsing Stencil Print Between Dips
-
TIPS FOR VARIOUS DYE PROJECTS
- Jul 26, 2023 Preventing Crocking and Dyeing Large Fabrics Like Bedding
- Jul 26, 2023 Using Fresh Goldenrod Leaves to Make a Paintable Dye Pigment
- Jul 26, 2023 Type of Wood for Making Block Prints
- Jul 26, 2023 Mordant Recipe: Block vs Screen Printing
- Jul 26, 2023 Making a Stamp Pad
- Jul 26, 2023 Dyeing with Fresh Plants
- Jul 26, 2023 Indigo Resist Screen Printing
- Jul 26, 2023 Destabilized AKA De-Fatted Bran in Rice Paste Resist
- Jul 25, 2023 Dipping Metal in my Vat
- Jul 25, 2023 Using Natural Indigo Paste
- Jul 25, 2023 Dyeing Vegetable Tanned Leather
- Jul 25, 2023 Tips for Using Rice Paste in a Ferrous Vat
- Jul 25, 2023 Dyeing Paper
- Jul 25, 2023 Chalk and Cheesecloth Clarification in Mordant and Block Printing
-
USING MORDANTS
- Jul 26, 2023 Mixing Mordant
- Jul 26, 2023 Mordant Recipe: Block vs Screen Printing
- Jul 26, 2023 Diluting Mordant Paste
- Jul 25, 2023 Chalk and Cheesecloth Clarification in Mordant and Block Printing
Is the Fermentation Vat the Best Vat?
Q: Is the Fermentation Vat the Best Vat?
A: This is an ongoing, developing manifesto on a pro-fermentation position - Last Updated September 20, 2022
Short answer, yes. The fermentation vat is the best vat that I’ve worked with.
If you’re new to the realm of indigo vats there’s some basic terminology to get under your belt. First is the term “vat”. It refers to a liquid solution which contains water, indigo pigment, something alkali and some sort of reducing agent which activates the indigo - allowing it to dye onto fabrics. Vats are typically described by the reducing agent which has been used - e.g. fructose vat (some sort of fruit sugars, whether gleaned from fruit pulp or purchased powder), ferrous vat (powered by iron), zinc-lime vat (you get it - powered by zinc and lime), thiox vat, etc. These vats are all of a type which are powered by their ingredients - if it stops working, you can simply add more of the ingredients (to a point), and things will get going again. I think of all these vats as ‘recipe’ vats - add some this, add some that and boom, you’re dyeing.
Over the past couple years, I’ve been working with fermentation vats - I think of these more as ‘relationship’ vats. I find the process similar to making and monitoring a sourdough starter, vinegar making from fruits or making kimchi or sauerkraut. Yes, there is an initial combination of the necessary ingredients, but following that combination - there is a daily practice - a relationship with the vat that develops where you can read the conditions of the vat and make appropriate decisions about how to keep it healthy.
I’m finding the distinction between ‘recipe’ and ‘relationship‘ to be essential.
The purpose of pursuing a natural dye practice is to engage more fully with the world around us. Over time, I’ve become more and more troubled by the popular, published approach to ‘natural’ dyeing and its reliance on a commercial/industrial apparatus to supply the materials and ingredients necessary. It has gnawed at me for years - my own lack of understanding of materials used in ‘natural’ dyeing. I believe myself to be quite informed on materials and processes - yet I found that so many of the ingredients called for in ‘natural’ dye are products of an industrial apparatus that I had close to zero understanding of their production and sources. Do you know what Slaked Lime is? Have you seen how it is produced? How about Alum? Ferrous sulfate? Any ‘natural’ dye extracts? Can you prove that those are actually what they say they are? Would you ever bother to do so? What portion of your dye ingredients do you know how to create? How much of your process is reliant on a system that you cannot see the workings of? How far away did these ingredients come from to reach you? Does it have to be like this?
I don’t think that natural dyeing is a solution to any ills of our contemporary industrial textile dyeing apparatus. Natural dye processes are traditionally very resource intensive - involving heavy water use as well as lots of combustion of hydrocarbons to heat liquids. I cannot conceive of a sustainable scale of production that would keep pace with the demands of the people - without being deleterious to the shared environment. I’d like to acknowledge natural dyeing’s actual current role in the ‘developed’ world. I believe the practice exists as a existential relief - an anathema to industrial systems.
The same yank - need to have control leads us to want to use crazy colors - and so requires the use of foreign extracts, extreme choices - rare foreign bugs, collected and shipped from thousands of miles away. Just admit - you may live in a boring place or way.
Indigo Vat Troubleshooting: No Longer an Odor
Q: My vat smelled really pungent when I first made it but now the smell is gone. Did something go wrong?
A: My guess is that all the active ingredients have probably settled to the bottom, try re-heating and sharpening if need be and see what happens!
Indigo Vat Troubleshooting: Dark Blue Vat
Q: My vat is dark blue and not dyeing correctly, any idea what is wrong?
A: If your vat is dark blue, it is under-reduced. Are you using a metal container? If you heat the vat up to 120F (or higher) you can force out some of the dissolved oxygen, and it should redevelop the coppery scum on top. Stir it, let the sediment settle out for at least a half hour, then do another round of dyeing. You can also follow my directions on sharpening on my website : http://www.grahamkeegan.com/indigo-vat-basics/
Indigo Vat Troubleshooting: Greenish Tint
Q: My vat has a greenish tint to it, is something wrong?
A: The vat should always have a greenish tint, though the oxidized indigo on your fabric should always appear blue. If there is a greenish tint there, you hit the sediment when you were dipping and your piece has got iron crud on it. You can wash with citric acid and soap alternatively until the piece goes back to pure blue. Avoid the sediment, but if you do get some on your piece, rinse it off immediately and THOROUGHLY.
Avoiding Fading
Q: I dyed several pieces in a ferrous vat and had great results. They came out with great deep blues. However, they have faded terribly since then. Any idea what I might be doing wrong?
A: The typical culprits on fading are:
Choice of material being dyed. Some materials have received inadequate preparation and have some sort of coating remaining on the fiber itself which keeps the indigo from dyeing directly to the cellulose. Well scoured materials will dye more evenly and will hold up to all kinds of wear (UV, Washing). Some fibers also just dye more easily. For example rayon is super easy to dye and linen is more challenging.
Conditions in the vat may have been under-reduced, meaning that the indigo was not in proper shape to adhere to the fabric.
Sediment layering. If your fabric hits the sediment on an early dip, future dips will adhere to the gunk layer you picked up from the sediment and then wash out later as the sediment itself eventually breaks down and moves along.
Waiting 24 Hours Between Mixing and Using Your Indigo Vat
Q: I have a question about the 24 hour waiting period from mixing the ingredients to using the vat. Could you tell me a little bit more about that. Is it necessary? I've used the Jacquard (synthetic) product and was able to use immediately after mixing.
A: In a word, yes. The wait is necessary. There is a big difference between the pre-reduced synthetic indigo and the natural indigo contained in the kit. The synthetic ingredients have already been modified to dissolve in water whereas the indigo in my kit does not dissolve in water. The 24 hour period allows the indigo to a) dissolve and b) become properly reduced (able to transfer onto fabric) and also c) the iron and lime in my kit (the activating ingredients) need time to properly combine. If you dye too soon, you'll get very pale blues and run the risk of staining the fabric brown/sludgy with the iron. If you wait the 24 hours, you'll get great color transfer and no staining.
Quantity of Indigo Paste in a Vat
Q: What quantity of indigo paste do I use to make a vat?
A: I recommend about 15g of the paste per gallon of liquid used to make the vat.
For a 5 gallon ferrous vat I use 60-75g of the paste, 100g iron and 150g lime. After dyeing for a while, I'll usually sharpen with a half dose (50g iron and 75g lime) to stretch out the vat a little bit and do some paler shades of blue.
Making a Long Term Vat
Q: I would like to have a large, permanent, natural indigo vat that I can upkeep and maintain. I’ve been buying kits but I don’t want to keep creating so much waste emptying and starting fresh every time the vat is exhausted. Do you have any input about what kind of vat is best? Or any pointers? I haven’t used your kit yet, but I am thinking of getting one - is it possible to use that as my base?
A: I’d recommend the ferrous vat (what’s in my kit and on my website) for a longer term vat. It is easy to maintain. Just make sure you AVOID THE SEDIMENT which will build up at the bottom of the vat over time as you sharpen it to maintain it. I’ve made Frankenstein’s monster style vats in the past (part fructose, part iron, part thiox). You can kind of just blend them together at will! The vat from my kit could certainly act as a starter. You’ll just have to dispose when you build up too much sediment to be able to dye what you want to dye cleanly and easily. If you’re going big, I recommend sourcing a steel 55 gallon drum. Though the investment in indigo and ingredients is much more in the beginning, they are actually much easier to use and maintain at that scale than a little 5 gallon guy.
Indigo Flower Comes and Goes
Q: I made a ferrous vat using your 1-2-3 instructions. I had a proper indigo flower upon completing the vat. But when I opened my vat this morning to use it the flower was gone except for just a few bubbles. Does this indicate a problem?
A: No problem! The flower should reform after proper stirring.
Using Pencil to Make Marks on Fabric - Does Graphite Affect the Vat?
Q: I am interested in using some stitched techniques to create patterns on my pieces. Everything I read tells me to use tailor's chalk or a disappearing water soluble fabric marker to plan out designs on my pieces, but I have been using pencil. Will the lead from my pencil affect my vat?
A: Graphite will not harm your vat but it is very challenging to remove from fabric so chalk is definitely better.
Under-Reduced Fructose Vat
Q: I have been dyeing in a fructose vat and no matter how many times I rinse my pieces the water still runs blue. Am I doing something wrong?
A: My guess is that the indigo in your vat isn’t fully reduced. Fructose vats are often “under-reduced” which means that the color is more weakly adhered to the fabric and thus rinses out more. You can just add new reducing ingredients to your old vat contents so you don’t waste the indigo though you’ll begin to build up more sediment which makes the dyeing more challenging (as you’ll need to make sure your fabric doesn’t get that material on it).
Troubleshooting a Different Vat Recipe
Q: Yesterday I tried an indigo iron vat recipe that was almost identical to yours, except it called for less of each ingredient (20g indigo, 40g ferrous sulphate, 60g lime) and it suggested starting with all of the water (nearly boiling) rather than 1 gallon and then topping it off. I used Stony Creek indigo 40%. After an hour it had the bronzy oily surface and the bubbles in the middle, so I thought it was good to go. However, it just stained the fabric a dull grey/blue rather than the characteristic green-to-blue change upon oxidation. Do you think it was because I didn't use enough ingredients? Or didn't let it sit long enough? Also, it was way too hot to submerge my hands into, is it ok to let it cool a few hours before dyeing?
A: My suggestion is to wait longer before dyeing. If it turns gray, you were most likely dyeing in the ‘unsettled’ sediment OR the indigo was not properly reduced yet. Allow the ingredients to settle out and the temperature to get cooler before you start dyeing.
Starting with all of the water boiling rather than heating only 1 gallon for mixing and then topping off after will not make a difference or lead to the challenges you are describing. You can even make your vat in completely cold water, it just effects the amount of time it will take for the indigo to properly reduce. When using hot water, proper reduction can happen in as little as one hour. When using cold water, proper reduction takes approximately 24 hours.
The ratio of ingredients is right on but those numbers seem low to be able to power a 5 gallon vat and that could also contribute to your difficulties. Don’t be afraid to add more iron and lime to get that indigo activated.
The vat will remain viable for quite a while after it is mixed up, days to weeks, depending on how well behaved you are with your fabric in the vat.
Avoiding Sediment
Q: I made a 5 gallon iron vat following the instructions on your website and I am trying to dye some cotton gauze scarves. The first one came out well but the rest have come out a grey/green - any thoughts on what I might be doing wrong? I am wondering if I am coming into contact with the sediment at the bottom of the vat? The only other time I dyed I was dipping in a 55 gallon drum so I didn’t have to worry much about the sediment and I am wondering if now that I’m using a smaller vat if my pieces are dragging in the sediment. Is there a way to protect against that?
A: Yes, it does sound like sediment is the issue. The ferrous vat has an iron-rich sediment, which when coming into contact with the fabric will stain it yellowish - and when that is layered with the indigo, a sludgy green. My suggestions would be to switch to a bigger/deeper container and avoid the sediment altogether or put some sort of bag/basket/strainer in the vat secured to the top of the container so that the pieces literally cannot touch the sediment. Also, make sure to not stir the vat beforehand on the same day it is used to dye. The sediment needs time to settle.
If you are dyeing in a steel pot, I recommend heating the contents up to about 120 and holding for an hour or so, stirring occasionally. This will revitalize the vat. Otherwise, you can reheat the contents with some sort of heating element or bucket wrap like this: https://www.amazon.com/dp/B00OYEABGQ/ref=biss_dp_t_asn
It may seem "expensive" but its amazing how much better a warm vat performs!
Indigo Vat Troubleshooting: Recipe Quantities for a Large Vat
Q: I am wondering if you are able to help me troubleshoot my vat. I made a 19 gallon iron vat in a plastic bin about a week ago with no success. I found instructions online that called for 20g indigo, 40g iron, and 60g lime for a 5 gallon vat, so I multiplied it by 4 for 19 gallons (80g indigo, 160g iron, and 240g lime). I see that this recipe has lower quantities of each than what you recommend and I am not sure why or if this is the issue. Initially the vat seemed to work. On the first day it had a coppery sheen but no flower and produced mid-dark blues. I dyed approximately 100g of fabric. On subsequent days, however, everything went downhill. I have continuously checked the pH, stirred, and added more iron and lime when I thought necessary. The vat liquid continues to be blue but I cannot get any good color when I dip. I tried restarting it by adding 1-2-3 solution again (as per your instructions). I am pretty sure the vat is not exhausted, but this still has not helped. I bought iron sulphate from a garden shop, it is ferrous (II) sulphate as far as I am aware. I am thinking of chucking out the vat and starting again by scaling up your recipe of 50g, 100g, 150g. Any thoughts?
A: No need to chuck! I'm going to assume that you actually have the right kind of iron, but definitely double check! It just sounds like your numbers are low for the vessel. I'd use at least 600g lime, 400g iron to properly reduce that amount of liquid (maybe more). If you've still got the vat, try decanting a gallon or two, heating to simmer, cut the heat then mix in another 450g lime and 300g iron (plus any additional indigo you may want). After ageing that for an hour or so (it will probably be a thick paste), add back to the large vat and stir thoroughly. It should dye well on the following day.
Sharpening Your Vat
Q: I'm wondering if you can keep an indigo and iron vat going by feeding it more after it’s exhausted of indigo or do you have to begin again from scratch once there's no indigo pigment left in it?
A: Yes, you can keep the vat rolling by "sharpening" it. Over time (after a couple rounds of sharpening) you will build up a bunch of sediment that will start to cling to the bottom of your fabrics and leave some "muddy" indigo tones. At this point, you do need to start from scratch, or just decant the clear liquid and discard the sediment, then top it up.
So, try adding all ingredients again in proportion. I decant some of the clear liquor (1-2 gallons) from the top of the vat into a stainless steel sauce pot that I've dedicated to dye use, heat to boiling, then remove from the heat and add the ingredients. Mix well (immersion blender without making bubbles if you've got one). Let that sit for a few hours until it is an insane neon yellow, then add back into the larger container.
Top up your vat with fresh, hot water to keep it near the brim.
You can then let it cool to ambient temperature and use as normal.
Stirring Your Vat
Q: Should I stir my ferrous vat every time before I use it?
A: I recommend letting your vat settle out at least an hour before dipping after the last time you’ve stirred. Stir when you finish a dye session. If you stir too close in time prior to dipping, the sediment will won’t have time to settle and you’ll get sediment on your piece, which is not ideal as it can tint your piece toward a ‘muddier’ indigo tone, but it can be rinsed off.
You can reference “Q: I am dyeing in a ferrous vat and got sediment from the bottom of the vat on my piece. Is that bad? What should I do?” to learn more about how sediment affects your piece and what you can do about it!
Also, when I stir it is usually for only 20-30 seconds and is only to get all the sediment up and moving around. There is no benefit to prolonged stirring, or stirring your vat when you aren’t preparing to dye in it, and in fact that is a great way to introduce oxygen into the vat which will weaken it.
Adding More Pigment to a Fresh Leaf Extraction Vat
Q: I made an indigo vat using fresh leaves. I used washing soda for pH and sodium hydrosulphite for reduction. The vat worked very well but the dye is all taken up now. Can I add more leaves to the vat to give it more pigment or must I start over with a new vat?
A: I’ve never added fresh leaves to an existing indigo vat, and can’t imagine that it would be a good way to go, what with the sediment, elevated pH and the dye already in the liquid. You can definitely extract the pigment from the leaves separately and add the extract to the vat though with additional pH adjusting and reducing agents to strengthen the existing vat.
Making a Vat for Pale Dyeing
Q: I am about to make a 5 gallon vat and I only want to use it to dye some pieces to a pale blue. Since I’m only wanting a pale color, can I reduce the amount of indigo paste I add to the vat so I don’t waste indigo? If so, how much indigo paste would you recommend using?
A: For pale blues, I'd recommend starting at 10g of indigo extract for a 5 gallon bucket, but still use 100g iron and 150g lime. This will make sure that the indigo is fully reduced and will add incremental pale shades to your pieces. You can paste up and add more indigo as that vat loses efficacy.
Sizing Up Your Vat
Q: I have never done an indigo vat in anything larger than a 5 gallon bucket. However, I was wondering about using a large trash can (32 gallons) for yardage. What are your thoughts? I was planning on doing a cold vat with iron and lime and have had great results in the 5 gallon. Do the proportions simply need to be multiplied by 6 to account for the size? Ex. if I used 50 grams of indigo in a 5 gallon vat, I would use 300 grams in a large vat. That just seems like so much indigo!
A: Yes, you can just increase the scale accordingly. It is quite a bit of indigo, but the vessel is very large! I work out of a 55 gallon vat right now and initially used a couple pounds of indigo to set it up. Make sure that you get a very heavy duty trash can, as they tend to warp and bend and are challenging to work with when full of water!
Indigo Vat Troubleshooting: Lye and Hydrosulfite
Q: I am using a Philippine indigo paste and the instructions say to melt 100 g of the paste in 10 litres of hot water and then add 1.25g / liter of sodium hydrosulfite and mix until incorporated and then add 1.25g / liter of sodium hydrosulfite and let sit for 20 minutes before dipping.
I followed these instructions but my vat does not seem to be working well. It is very liquidy and weird and a pale blue. Do you have any suggestions for fixing this vat?
A: As an initial matter I would check to see how new your stock of Lye and Hydrosulfite are as they can become less effective if they're aged and oxidized.
I'd guess by your description that your vat was under-reduced (the liquid being blue and dull) which means I'd recommend adding more of the NaOH and Hydrosulfite. I usually add those together into a cup full of simmered water until they are completely dissolved, then incorporate that into the vat, stir the whole thing and check back in half an hour to see where you're at.